10 Problems You Often Encounter in the Flotation Process
The flotation process is often used in processing minerals. However, we often encounter many problems in the flotation process, and the flotation effect is not good. So, I have some problems, could you help me solve them?
Of course. Flotation separation process has strict rules for grinding particle size, pulp density, and flotation reagents. Therefore, we strongly recommend that you should know about the flotation conditions of minerals, such as gold ore and copper ore.
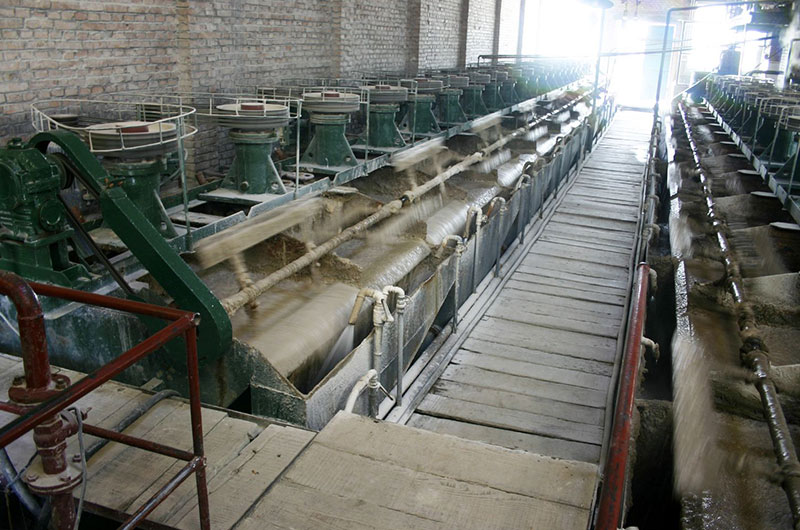
1. What is the effect of grinding particle size on flotation?
Too coarse ore particles (greater than 0.1mm) and very fine ore particles (less than 0.006mm) do not float well, and the recovery rate is low.
In the flotation of coarse particles, due to the larger weight, the shedding force of the ore particles increases. So, you need:
- (1) Use a sufficient amount of the most effective collector.
- (2) Increase the aeration of pulp to cause larger bubbles, and increase the amount of microbubbles precipitated in the water.
- (3) The stirring intensity of pulp should be appropriate.
- (4) Properly increase the pulp concentration.
- (5) The scraper should be quick and steady when scraping the bubbles.
In the flotation of fine particles (refers to slime less than 5-10μm):
- (1) Due to the small quality of the slime, it is easy to adhere to the surface of coarse particles, which reduces the floatability and deteriorates the selectivity.
- (2) Due to the large specific surface of sludge, they will absorb a large amount of flotation reagents in the pulp, which reduces the reagent concentration in the pulp, destroys the normal flotation process, and reduces the flotation index.
- (3) Because the slime is very fine and has a large surface area, the surface activity is increased. It is easy to act with chemicals and not easy to be sorted so that the foam is too stable. Then it causes difficulty in the selection, resulting in lower quality of concentrate and lower concentration efficiency of foam products.
2. How to prevent and reduce excessive slime in pulp?
- (1) Reduce and prevent the formation of ore slime: Adopt a multi-stage grinding process and a stage beneficiation process. It is necessary to correctly select grinding and classifying equipment to improve the classifying efficiency.
- (2) Add reagents to eliminate the harmful effects of ore slime: water glass, soda and caustic soda are commonly used, which can reduce the flocculation cover effect of ore slime. To reduce the harmful effects of a large amount of adsorbents in the sludge, the method of adding drugs in stages is adopted.
- (3) Deslime the ground ore before flotation and discard it as tailings. If the content of useful components in the slime is high, the removed slime can also be treated by flotation alone, or sent to water for smelting treatment.
How to deslime?
- (1) Desliming by a classifier.
- (2) Desliming with hydrocyclone.
- (3) A small amount of foaming agent can be added before flotation to remove the easy-floating sludge.
3. How to float the coarse ore particles?
Why is the flotation of coarse ore particles so difficult?
Coarse grinding can save grinding costs. To ensure the recovery rate of roughing, some flotation plants tend to reduce the fineness of rough grinding.
However, as the coarse grains are relatively heavy, it is difficult for coarse grains to float, and the chance of collision with air bubbles is reduced. After the coarse grains are attached to air cells, they are easily removed from the air cells. Therefore, the coarse grains have a poor floatation effect.
How to improve the effect of coarse flotation?
- (1) Use collectors with strong collecting power, and add auxiliary collectors like kerosene and diesel oil to strengthen the collection of coarse grains.
- (2) Appropriately increase the mass fraction and buoyancy of the pulp. Ensure the stability of foam layer and stir to promote the suspension of coarse grains and increase the chance of adhesion with air bubbles.
- (3) Appropriately increase the air volume of the flotation machine to form large bubbles. The bubbles gather into a "buoyancy", making the coarse grains obtain greater buoyancy and float.
- (4) Use a shallow tank flotation machine, which can shorten the floating distance of bubbles and reduce the ore particles falling off from the bubbles. Or use a special flotation machine for coarse grains like the XJK flotation machine and SF flotation machine.
- (5) Use a rapid and stable foam scraping device. It can scrape the floating mineralized foam in time to reduce the ore particles falling off again.
4. How to float the fine-grained materials?
1. Why is the flotation of the fine-grained materials so difficult?
- (1) The specific surface area of fine particles is large, and the surface energy is significantly increased. Under certain conditions, non-selective mutual coagulation easily occurs between the surfaces of different minerals. Besides, the large surface energy results in poor selective adsorption, making it difficult to selectively separate the fine particles.
- (2) The volume and quality of fine particles are small, and the possibility of collision with air bubbles is small. Even when they collide with bubbles, it is difficult to overcome the resistance of the hydration layer between ore particles and bubbles, making it difficult to adhere to the bubbles.
How to float the fine-grained materials?
- (1) Selective flocculation and flotation. Use flocculant to flocculate the target ore particles or gangue fine mud, and then use flotation to separate.
- (2) Carrier flotation. Use the ore particles of general flotation size as the carrier to cover the fine particles of the target mineral and float. The carrier can use the same or different kinds of minerals. For example, fine-grained gold can be floated using pyrite as a carrier. The fine-grained iron and titanium impurities in kaolin can be floated using calcite as a carrier.
- (3) Agglomeration flotation (emulsion flotation). This method has been used for fine-grained manganese ore, ilmenite, and apatite. The collector and neutral oil can be made into an emulsion first, and then added to the pulp. It is also possible to add neutral oil and collector separately to the pulp of high-quality fraction (solid content up to 70%), stir vigorously, control the time, and then scrape out the upper foam.
5. What is the impact of slime on flotation and how to solve it?
Too much sludge will bring a series of adverse effects to the flotation:
- (1) Easy to be mixed in foam products, which will reduce the concentrate grade.
- (2) Easy to cover the surface of coarse grains and affect the flotation effect.
- (3) Adsorb a large amount of reagents and increase medicine consumption.
- (4) Make the pulp sticky and the aeration conditions deteriorate.
How to solve it?
- (1) Use the thinner pulp to reduce the viscosity of pulp and the inclusion of mineral sludge in the foam product.
- (2) Add dispersant to disperse ore slime and eliminate the harmful effect of ore slime covering the surface of other minerals.
- (3) Add reagents in batches to reduce the chemicals consumption.
- (4) Deslime the materials before flotation.
The commonly used desliming method is cyclone classification desliming.
6. What is the impact of air on flotation?
In addition to oxygen, nitrogen, and inert gases, there are carbon dioxide gas and water vapor in the air.
Air has certain effects on mineral floatability:
- (1) When the mineral is broken and exposed to the fresh surface, it will be hydrated when it encounters water, and it will be hydrophilic. However, when the gas is adsorbed to the mineral surface, it can weaken the hydration, resulting in the initial hydrophobicity of the surface.
- (2) The use of gas and mineral surfaces is selective. Oxygen has a greater impact on the mineral surface.
- (3) The role of oxygen is beneficial to the hydrophobicity of sulfide ore. However, if the action time is too long, the mineral surface will become hydrophilic. When the gas adsorption conditions are suitable, the mineral surface will be hydrophobic and can be floated even without flotation agent (such as dry coal powders). And galena can only float up after the initial action of oxygen.
7. What is the impact of slurry stirring?
Enhanced aeration and agitation are beneficial to flotation:
- (1) Promote the suspension and uniform dispersion of ore particles in the tank.
- (2) Promote a good dispersion of air to make it evenly distributed in the tank.
- (3) Promote air to strengthen the dissolution in the high-pressure area in the tank and strengthen the precipitation in the low-pressure area to create a large number of active microbubbles.
However, excessive aeration and agitation can lead to bad effects:
- (1) Promote the merger of bubbles.
- (2) Reduce the concentrate quality.
- (3) Increase the power consumption.
- (4) Increase the wear of the flotation machine.
- (5) The volume of slurry is reduced (as the volume of tank occupied by the bubbles increases).
- (6) Cause the ore particles attached to the bubbles to fall off.
In production, the amount of aeration and agitation should be determined through tests according to the flotation machine's types and features.
8. What effect does the pulp density have on flotation index?
- (1) Affect the recovery rate. When the pulp density is small, the recovery rate is low; when the pulp density increases, the recovery rate increases. But the recovery rate exceeds the limit, the recovery rate will decrease, as the too high density will destroy the aeration conditions of the flotation machine.
- (2) Affect the concentrate quality. The thinner pulp yields higher concentrate quality, while thicker pulp reduces the concentrate quality.
- (3) Affect medicine consumption. When the pulp is thicker, the dosage per ton of ore is less, and when the pulp density is thinner, the dosage per ton of ore is increased.
- (4) Affect the productivity. As pulp density increases, so does the productivity.
- (5) Affect water and electricity consumption. The thicker the pulp, the smaller the water and electricity consumption.
- (6) Affect the flotation time. The thicker pulp has a longer flotation time.
In short, the pulp density should be appropriate. The thicker pulp is beneficial to the flotation, but too thick density will reduce the concentrate quality and recovery rate.
9. Pulp density, flotation conditions and ore properties
The pulp density is related to the ore properties and flotation conditions.
- (1) The thicker pulp is used for minerals with high flotation density, while the thinner pulp is used for minerals with low flotation density.
- (2) The thicker pulp is used for flotation of coarse-grained materials, while the thinner pulp is used to float fine-grained and muddy materials.
- (3) The thicker pulp is used for roughing and sweeping, which can reduce the reagent consumption and the number of flotation machines, while the thinner pulp is used for the selection to obtain the high-quality concentrate.
The pulp density is 25%-35% during roughing, and 10%-20% for flotation of fine-grained ores with high mud content.
10. What is the impact of pulp mass fraction on flotation?
The mass fraction of the ore pulp is very important for the flotation separation.
Two ways can express the pulp mass fraction:
- (1) Liquid-solid ratio represents the ratio of liquid to solid mass (or volume) in the pulp. It is convenient for the calculation of the pulp process.
- (2) Percentage of solid content represents the percentage of solid mass (or volume) in the pulp. It is widely used in the mineral tests and production.
The effect of the pulp mass fraction on flotation:
- (1) Recovery rate. When the pulp mass fraction is low, the recovery rate is low; when the pulp mass fraction increases, the recovery rate increases. Therefore, the pulp mass fraction should not be too large, otherwise, the flotation machine will be difficult to aerate normally in the pulp and reduce the recovery rate.
- (2) Concentrate grade. The thinner pulp can produce the higher-grade concentrate, while the thicker pulps produce the low-quality concentrate.
- (3) Dosage of flotation reagent. The reagent must maintain a certain mass fraction to have a good flotation effect. When the pulp is thicker, the mass fraction of the reagent increases. That is, the required mass fraction of the reagent can be achieved with less agent. When the pulp is thinner, the reagent dosage increases.