What is a vertical roller mill?
The vertical roller mill (VRM), also known as the vertical grinding mill, is a large-scale powder mill equipment developed by FTM Machinery using advanced powder grinding and external circulation technology.
It can grind materials with Mohs hardness below 8 and humidity below 15%, such as cement raw materials, cement clinker, coal, slag, limestone, iron ore, gypsum, marble, phosphate ore, lithium ore, dolomite rock, kaolin clay, bentonite, talc, graphite, etc.
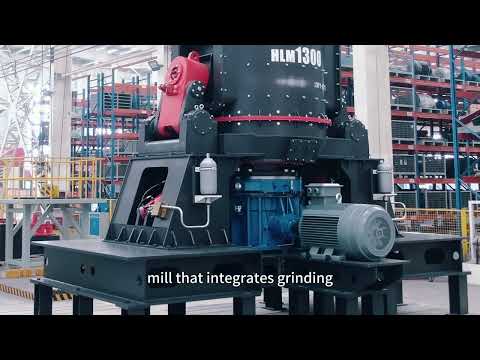
Vertical mills offer high output, stable quality, and energy efficiency compared to other types of grinding mills. Using hydraulic pressure, they grind, classify, and dry materials efficiently, serving industries like cement, power, metallurgy, chemicals, and non-metallic minerals.
Vertical roller mills for sale
To meet market demand, FTM Machinery offers various vertical mills. Based on different materials, the popular mill types are the vertical cement mill, vertical coal pulvertizer mill, slag vertical mill, vertical mineral grinding mill, and ultra-fine vertical mill.
1. Vertical cement mill
In the production cost of cement plants, the consumption of grinding powder can account for 40%. Therefore, the cement vertical mill has become a key equipment in cement plants. It helps to control the quality of cement and improve the qualified rate of products.
Raw materials: Cement raw materials and clinker, such as limestone, gypsum, clay, sandstone, etc.
Material moisture: ≤5%
Finished product moisture: ≤1–3%
Capacity: 8–420 t/h
View the detailed parameters of the cement mill:
- HLM cement vertical mill
- HLM clinker pre-grinding vertical mill
Specifications | Capacity(t/h) | Specific surface area | The raw material moisture | The finished product moisture | Main motor power(kW) |
HLM19S | 8-13 | ≥380㎡/kg | ≤5% | ≤1% | 280-315 |
HLM21S | 11-18 | 400-450 | |||
HLM24S | 15-20 | 500-560 | |||
HLM28S | 28-35 | 900-1000 | |||
HLM35S | 70-80 | 1800-2000 | |||
HLM42S | 95-110 | 2500-2800 | |||
HLM46S | 130-150 | 3150-3800 | |||
HLM53S | 160-200 | 4500-5000 |
Note: The grindability (Bond) index of raw materials is less than or equal to 18kw/t
Specifications | Capacity(t/h) | Main motor power(kW) |
HLM19S | 8-13 | 280-315 |
HLM21S | 11-18 | 400-450 |
HLM24S | 15-20 | 500-560 |
HLM28S | 28-35 | 900-1000 |
HLM35S | 70-80 | 1800-2000 |
HLM42S | 95-110 | 2500-2800 |
HLM46S | 130-150 | 3150-3800 |
HLM53S | 160-200 | 4500-5000 |
Note: The grindability (Bond) index of raw materials is less than or equal to 18kw/t
Specifications | Capacity(t/h) | Product fineness | The raw material moisture | Main motor power(kW) | |
≤80μm | ≤2mm | ||||
HLM17-2Y | 12-20 | ≥30% | ≥90% | ≤3% | 200 |
HLM19-2Y | 18-25 | 280 | |||
HLM21-2Y | 25-35 | 400 | |||
HLM24-2Y | 30-45 | 500 | |||
HLM28-2Y | 60-80 | 900 | |||
HLM35-3Y | 125-165 | 1800 | |||
HLM42-4Y | 200-230 | 2500 | |||
HLM46-4Y | 250-300 | 3150 | |||
HLM53-4Y | 360-420 | 4500 |
Note: The grindability (Bond) index of raw materials is less than or equal to 18kw/t
Specifications | Capacity(t/h) | Main motor power(kW) |
HLM17-2Y | 12-20 | 200 |
HLM19-2Y | 18-25 | 280 |
HLM21-2Y | 25-35 | 400 |
HLM24-2Y | 30-45 | 500 |
HLM28-2Y | 60-80 | 900 |
HLM35-3Y | 125-165 | 1800 |
HLM42-4Y | 200-230 | 2500 |
HLM46-4Y | 250-300 | 3150 |
HLM53-4Y | 360-420 | 4500 |
Note: The grindability (Bond) index of raw materials is less than or equal to 18kw/t
2. Vertical coal pulverizer mill
The vertical coal pulverizer mill is also known as a vertical coal mill. It is used to pulverize (crush and grind) coal into fine powders that is need for combustion or processing.
Raw materials: Coal, coal gangue, lignite, bituminous coal, coal slime, coke, carbon black, fly ash, etc.
Coal moisture: ≤15%
Powder moisture: ≤1–5%
Capacity: 6–80 t/h
View the detailed parameters of the coal mill:
Specifications | Capacity(t/h) | Pulverized coal fineness | The raw coal moisture | Pulverized coal moisture | Main motor power(kW) |
HLM1200M | 6—10 | R0.08=5-15% | ≤15% | ≤1-5% | 110-132 |
HLM1300M | 10-15 | 160—200 | |||
HLM1500M | 15—20 | 220—280 | |||
HLM1700M | 20-30 | 280-355 | |||
HLM1900M | 26-35 | 355—450 | |||
HLM2200M | 35-50 | 450—560 | |||
HLM2400M | 45-55 | 560-710 | |||
HLM2800M | 60-80 | 900—1120 |
Note: Raw coal HGl≥55
Specifications | Capacity(t/h) | Main motor power(kW) |
HLM1200M | 6—10 | 110-132 |
HLM1300M | 10-15 | 160—200 |
HLM1500M | 15—20 | 220—280 |
HLM1700M | 20-30 | 280-355 |
HLM1900M | 26-35 | 355—450 |
HLM2200M | 35-50 | 450—560 |
HLM2400M | 45-55 | 560-710 |
HLM2800M | 60-80 | 900—1120 |
Note: Raw coal HGl≥55
3. Slag vertical mill
Slag vertical mills are specially designed to process slag (a by-product of metal smelting, especially slag from blast furnaces in steel plants). The ground slag can be made into cement, concrete or roadbed materials.
Raw materials: Slag, steel slag, blast furnace slag, metallurgical waste slag, ceramic waste, etc.
Slag moisture: ≤15%
Final moisture: ≤1%
Capacity: 6–165 t/h
View the detailed parameters of the slag vertical mill:
Specifications | Capacity(t/h) | Specific surface area | Slag moisture | Mineral moisture | Main motor power(kW) |
HLM17-2N | 6-10 | ≥420㎡/kg | ≤15% | ≤1% | 200-220 |
HLM19-2N | 8-13 | 280-315 | |||
HLM21-2N | 10-15 | 400-450 | |||
HLM24-2N | 12-18 | 500-560 | |||
HLM28-2N | 22-30 | 900-1000 | |||
HLM35-3N | 55-70 | 1800-2000 | |||
HLM42-4N | 70-100 | 2500-2800 | |||
HLM46-4N | 85-135 | 3150-3800 | |||
HLM53-4N | 130-165 | 4500-5000 |
Note: Slag grindability (Bond) index ≤25kw/t; Steel slag grindability (Bond) index ≤30kw/t; The production of steel slag is reduced by about 30-40% when it is ground.
Specifications | Capacity(t/h) | Main motor power(kW) |
HLM17-2N | 6-10 | 200-220 |
HLM19-2N | 8-13 | 280-315 |
HLM21-2N | 10-15 | 400-450 |
HLM24-2N | 12-18 | 500-560 |
HLM28-2N | 22-30 | 900-1000 |
HLM35-3N | 55-70 | 1800-2000 |
HLM42-4N | 70-100 | 2500-2800 |
HLM46-4N | 85-135 | 3150-3800 |
HLM53-4N | 130-165 | 4500-5000 |
Note: Slag grindability (Bond) index ≤25kw/t; Steel slag grindability (Bond) index ≤30kw/t; The production of steel slag is reduced by about 30-40% when it is ground.
4. Vertical mineral grinding mill
The vertical mineral grinding mill is used for fine and ultra-fine grinding of minerals and rocks. It produces uniform powder through vertical grinding for mining, metallurgy, building materials, and chemical industries.
Raw materials: Minerals and ores, such as iron ore, phosphate ore, quartz, dolomite rock, bentonite, garnet, etc.
Final moisture: ≤1%
Powder fineness: 0.84–0.37 mm (20–400 mesh)Capacity: 10–320 t/h
View the detailed parameters of the mineral grinding mill:
Specifications | Capacity(t/h) | The finished product fineness | The raw material moisture | The finished product moisture | Main motor power(kW) |
HLM1300K | 10-40 | 0.84-0.37mm (20-400 mesh) | ≤15% | ≤1% | 200 |
HLM1500K | 13-50 | 280 | |||
HLM1700K | 18-70 | 400 | |||
HLM1900K | 20-85 | 500 | |||
HLM2200K | 35-135 | 800-900 | |||
HLM2400K | 40-160 | 900-1120 | |||
HLM2800K | 50-200 | 1120-1250 | |||
HLM3400K | 70-260 | 1800-2000 | |||
HLM3700K | 90-320 | 2500-2800 |
Note: The grindability (Bond) index of raw materials is less than or equal to 13kw/t
Specifications | Capacity(t/h) | Main motor power(kW) |
HLM1300K | 10-40 | 200 |
HLM1500K | 13-50 | 280 |
HLM1700K | 18-70 | 400 |
HLM1900K | 20-85 | 500 |
HLM2200K | 35-135 | 800-900 |
HLM2400K | 40-160 | 900-1120 |
HLM2800K | 50-200 | 1120-1250 |
HLM3400K | 70-260 | 1800-2000 |
HLM3700K | 90-320 | 2500-2800 |
Note: The grindability (Bond) index of raw materials is less than or equal to 13kw/t
5. Ultra-fine vertical mill
The ultra fine vertical mill is ideal for small and medium-sized powder grinding plants. It can handle materials with Mohs hardness smaller than 4 and output of 2–45 tons/hour. The milling powder has good fineness and high quality.
Raw materials: Fluorite, limestone, marble, calcite, apatite, gold ore, clay, gypsum, talc, etc.
Final moisture: ≤1%
Output size: 10–40 μm (370–1,250 mesh)
Capacity: 2–45 t/h
View the detailed parameters of the ultra-fine vertical mill:
Specifications | Feed particle size(mm) | Capacity(t/h) | Product fineness | The raw material moisture | Main motor power(kW) |
HLM1200X | ≤10 | 2-6 | Screen passing rate of 10-40μm 97% | ≤4% | 132 |
HLM1300X | ≤10 | 3-10 | 220 | ||
HLM1500X | ≤10 | 4-13 | 315 | ||
HLM1700X | ≤15 | 7-18 | 450 | ||
HLM1900X | ≤15 | 8-23 | 560 | ||
HLM2200X | ≤20 | 13-35 | 800 | ||
HLM2400X | ≤20 | 15-45 | 1000 |
Note: Mohs hardness grade 4 or below
Specifications | Feed particle size(mm) | Capacity(t/h) | Main motor power(kW) |
HLM1200X | ≤10 | 2-6 | 132 |
HLM1300X | ≤10 | 3-10 | 220 |
HLM1500X | ≤10 | 4-13 | 315 |
HLM1700X | ≤15 | 7-18 | 450 |
HLM1900X | ≤15 | 8-23 | 560 |
HLM2200X | ≤20 | 13-35 | 800 |
HLM2400X | ≤20 | 15-45 | 1000 |
Note: Mohs hardness grade 4 or below
Main parts of the vertical roller mill
The vertical grinding mill has a simple vertical structure, occupying about 50% of the floor space of ball mill. FTM Machinery adopts a modular design to help users replace vertical milling machine parts quickly.
Roller mill diagram
The vertical roller mill parts mainly consist of the grinding rollers, grinding table, separator, mill stand, hydraulic system, gearbox, and other key parts.
1. Grinding roller
Grinding rollers (usually 2–4) are the core of a vertical mill, distributed on the grinding table. They are directly involved in the grinding of materials and are most susceptible to wear. The rollers are made of wear-resistant cast steel, alloy steel, or ceramic coating.
The vertical rollers are tilted to increase the contact area and improve the grinding efficiency. It can also prevent large materials from falling from the edge and blocking the air inlet.
2. Grinding table
The grinding table, or millstone, is a key vertical mill component. It is a flat or conical surface used to support the weight of the material being ground and the grinding material.
The grinding table is made of cast steel or cast iron. It is designed with a specific pattern of grooves or ridges to enhance grinding efficiency.
3. Separator
The separator, or classifying wheel, separates the ground material from the unground material. It is located above the grinding table and consists of a rotor with blades that rotate around a central axis.
The separator is adjustable to control the particle size. The separated fine powder is sent to a storage system, while the coarse material is recycled for further grinding. The powder fineness is regulated by the separator speed and the gas flow through the mill.
4. Hydraulic system
The hydraulic tension system is used to apply the required pressure between the grinding rollers and the millstone. It typically consists of hydraulic cylinders, accumulators, and a hydraulic power unit.
The hydraulic cylinder is equipped with a nitrogen gas bag to absorb the vibration during the operation of the mill. It reduces energy consumption by 30%–50%.
5. Mill stand
The mill stand provides structural support and stability to the grinding mill. It is often made of heavy-duty steel or cast iron to withstand the mechanical forces generated during the grinding process.
Working principle of the vertical roller mill
A complete vertical mill powder production line consists of crushing, grinding, grading, dust removal, and other processes. The vertical grinding mill is the core grinding mill, as it directly affects the fineness, purity, and quality of the powder.
The vertical mill powder production line
After the material is crushed, it enters the vertical mill. The roller mill works on the principle of material bed grinding.
- 1The motor drives the grinding table to rotate, and the material falls from the feed inlet to the center of the millstone. At the same time, the hot air enters the mill from the air inlet. The heat generated evaporates the moisture in the material to achieve a drying effect.
- 2Under the action of centrifugal force, the material moves to the edge of the millstone, and when it passes through the annular groove on the grinding table, it is crushed by the grinding rollers.
- 3The airflow carries the ground material to the separator, where the fine particles are separated and collected as the final product.
Watch the following video to understand how the vertical mill works.
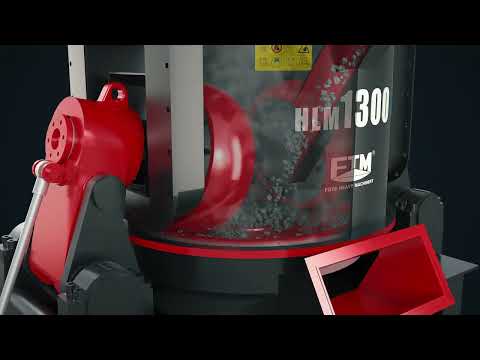
Why choose FTM Machinery vertical roller mills?
Vertical grinding mill is a common mining powder mills equipment. Compared with the traditional grinding mill machine, its advantages are more obvious:
- High grinding efficiency: The roller grinding area is large, and the grinding force is increased by hydraulic pressure to improve the grinding efficiency. The output is large, up to 420 tons per hour.
- Good product quality: The material stays in the grinding mill for a short time, reducing repeated grinding and ensuring stable product quality. The dynamic classifier is used to ensure a 97% screening rate and uniform powder size.
- Strong drying capacity: Direct contact with internal hot air enables effective drying of materials, with controllable temperature and moisture reduced from 15% to 1–5%.
- Eco-friendly: The mill operates under full negative pressure with reliable sealing and no dust leakage. The dust collector captures 99.9% of particles, and energy consumption is 30–50% lower than a ball mill.
- Low investment cost: Simple process, small footprint. The vertical mill allows outdoor installation, cutting construction costs. With drying and easy maintenance, the total investment is only 70% of a ball mill system.
- High automation degree: The fully automatic control system can realize remote control, and is easy to operate. The external independent thin oil lubrication station is convenient for oil replacement.
Customer cases
1. Vietnam clean coal pulverizing plant
With the emergence of vertical roller mills, clean energy pulverized coal is increasingly replacing traditional boiler coal. In July 2022, a Vietnamese customer began building a coal powder pulverizing plant with an annual output of 300,000 tons.
To meet the needs of customers, the pulverization of coal is equipped with 3 coal pulverizer mills, each with a capacity of 30 tons/hour.
To meet the needs of customers, we have equipped them with 3 vertical coal mills, each with a capacity of 30 t/h.
- Materials: Anthracite, lignite
- Capacity: 300,000 tons per year
- Feed particle size: ≤25 mm
- Output pulverized coal size: 200 mesh
- Equipment: 3 sets of HLM1900M coal vertical mills
- Auxiliary equipment: Jaw crusher, conveyor belt, quantitative feeder, dust collector
Vietnamese customers are very satisfied with the pulverized coal process. The pulverized coal is then processed into efficient clean coal power for use in large steel mills, power plants, and coal-fired plants.
2. Russian quartz powder grinding plant
As glass, photovoltaic, and ceramic industries grow rapidly, demand for quartz powder is rising. To support high-end manufacturing, Russia planned a quartz grinding plant last year, choosing two vertical mills for purity and particle size control.
- Material: Quartz stone
- Capacity: 120 tons/hour
- Feed particle size: ≤20 mm
- Output pulverized coal size: 325 mesh (D97≤44μm)
- Equipment: 2 sets of HLM1900K mineral vertical mills
- Auxiliary equipment: Jaw crusher, cone crusher, dust collector, classifier
After the project launched, the vertical mills ran stably, producing high-purity, well-sized quartz. The product was popular in the glass and photovoltaic industries, laying the foundation for its development in high value-added markets.
Frequently asked questions about vertical roller mills
1. Vertical roller mill VS ball mill: which is better?
- As the best-selling types of grinding mills (especially in the cement industry), the vertical roller mill and ball mill machine are very different:
- a. Grinding method: Vertical mills use vertical rollers to crush material on a grinding table, ideal for dry grinding. Ball mills grind by rotating ceramic or steel grinding balls and support both dry and wet grinding.
- b. Powder fineness: Vertical mills achieve up to 1250 mesh with finer and uniform particles. Ball mills typically produce 20–200 mesh powders.
- c. Energy efficiency: Vertical roller mills use a hydraulic system and drying system, cutting energy use by 30–50% compared with the ball mills.
- d. Structure: The vertical mills are the space-saving vertical structures, while the industrial ball mills are horizontally structured and easier to install in varied environments.
2. How to choose the right model for a vertical grinding mill?
- a. Feed size: Consider the maximum feed size of the material, which should be within the specified range of the mill.
- b. Required fineness: Determine the particle size of the ground material. Different mills have different fineness levels.
- c. Production capacity: Assess the required capacity based on the material amount to be processed per hour or day.
- d. Space constraint: Take into account the available space for the mill installation and footprint.
3. What affects the working efficiency of a vertical roller mill?
- a. The hardness of the grinding material. If the material is too hard, it will be more difficult to grind the powder, which will easily cause wear and tear on the equipment.
- b. The temperature of the material entering the mill. If the temperature is high, coupled with the impact of the grinding body, the temperature inside the mill will be too high, and the phenomenon of ball sticking will occur.
4. How to avoid wear on the grinding roller and millstone?
- a. Understand the grindability of the raw material. Too hard materials will cause serious wear to the lining of the grinding roller and millstone.
- b. Keep the centerlines of the four grinding rollers at the same horizontal line and the limit heights are the same.
- c. Prevent metal foreign matter from entering the mill, and use the iron remover of the system well.
- d. Regularly maintain the mill and clean debris remaining in the grinding table.