From the blog Interesting Facts You Should Know about Barite, we learned that barite is an important non-metallic mineral with a wide range of industrial uses. It needs to undergo beneficiation processes to achieve its various uses.
Barite is often associated with minerals such as quartz, calcite, dolomite, fluorite, siderite, rhodochrosite, pyrite, galena and sphalerite. In some metal deposits, such as lead, zinc, gold, silver and rare earth deposits, barite is often a common gangue mineral.
Therefore, the beneficiation process of barite is restricted by factors such as deposit type, mineral composition, and characteristics of barite and gangue phases.
In an efficient barite processing plant, barite ore needs to go through processes such as crushing, screening, and beneficiation. Each process will vary slightly based on the above factors.
Barite Crushing Process
Barite is brittle and fragile, so we often use jaw crushers for primary crushing. A good crushing effect will be obtained by using jaw crushers alone. Sometimes, cone crushers will be added for fine crushing.
To fully dissociate useful barite minerals, ball mills are commonly used to grind barite rocks.
Generally, the grinding fineness of barite-200 is 85~90%, and a two-stage grinding process is often used.
In view of the differences in the properties of barite ores, the optimum grinding fineness needs to be determined experimentally.
Barite Screening Process
The particle size of ground barite ores varies, and the barite beneficiation equipment has its own required feed particle size range, so screening equipment plays a vital role in selecting the ores with qualified particle size.
When screening barite ores, use a vibrating screen. It has a low failure rate, large processing capacity, high screening efficiency, and easy operation. It is an ideal machine for screening barite ore.
Barite Beneficiation Process
Crushed and ground barite ore undergoes simple beneficiation methods to separate the mineral from the waste rocks. Methods such as gravity separation, magnetic separation, and flotation are used.
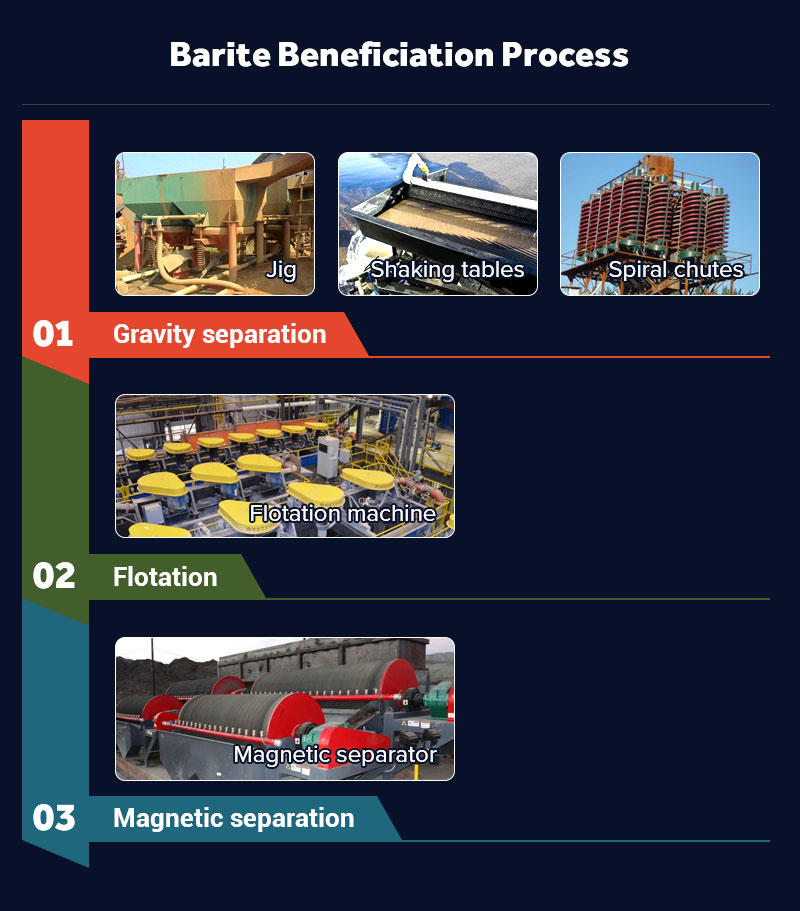
Barite Ore Gravity Separation
Gravity separation is often used to separate barite with high specific gravity from gangue minerals with low specific gravity, such as calcite, dolomite, quartz, or shale. For example, some flotation tailings and barite-fluorite associated ore can be recovered by gravity separation.
The available machines are jigs, shaking tables, and spiral chutes.
When processing barite ore with a particle size greater than 2mm, use the jigs.
When processing barite ore with a particle size smaller than 2mm, use shaking tables or spiral chutes.
Here is a case of barite gravity beneficiation.
Barite Ore Flotation
Flotation is an important way to recover barite from low-grade ores, associated ores and tailings. And it has good adaptability to various types of inlaid and complex barite ore, and is also an effective way to recover fine-grained barite.
The commonly used barite flotation methods include positive flotation and reverse flotation.
Positive flotation
Positive flotation usually uses fatty acid as a collector to flotate barite, suppresses gangue minerals such as fluorite, quartz and calcite with sodium silicate, etc., and recovers barite under weak alkaline (pH8-9) conditions.
Reverse flotation
Reverse flotation usually flotates sulfides or other easily floating minerals, suppresses barite, and the final tailings are barite concentrates.
The flotation machine is widely used for barite flotation.
Barite Ore Magnetic Separation
When there is a significant difference in the magnetic properties of the minerals, the magnetic separation process can be used for separation.
Barite is a non-magnetic mineral. When magnetic minerals (such as iron oxides) are the main gangue minerals, the magnetic separation process can be used to separate barite and gangue minerals. The resulting concentrate has a high BaSO4 content, which can be used as a requirement. Barite raw material for barium-based pharmaceuticals with very low iron content.
Magnetic separation is often used to select pyrrhotite, magnetite, limonite and hematite.
For barite ore containing magnetic iron minerals with fine particle size, strong magnetic separation is often used to separate iron-containing minerals and barite.
The magnetic separator is the core machine of the magnetic separation process.
Here is a case of barite gravity-magnetic separation.
For associated ores, flotation tailings, and ores with fine-grained mineral inlays that are difficult to recover, the recovery of barite by a single gravity or magnetic separation process is not enough, and a combined process is required to efficiently recover barite.
Common combined processes are: flotation-gravity separation, gravity-magnetic separation, magnetic-flotation separation, and magnetic-gravity-flotation separation.
After beneficiation, we get high-grade barite concentrates. We can sell it directly or we can grind it into ultrafine powder and sell it to oil exploration companies, filler companies, etc. In the next blog, I will share with you how to choose the right barite grinding mill.